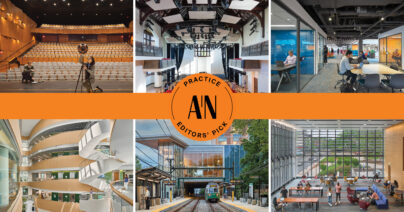
Acentech wins AN Best of Practice Award
Acentech is honored to be awarded an Editors’ Pick in The Architect’s Newspaper 2025 Best of Practice Awards in the Acoustic Consultant/Engineer category! This recognition highlights…
Sign up to stay connected with the latest Acentech news, industry alerts, seminar announcements, and blog posts. We know your inbox is precious, we promise never to spam you!